Low Cost Tooling Tool Design |
● Mold Tool Production
We make great tools for low-volume manufacturing. When making your mold tool we use pre-hardened tool steels such as P20 and NAK-80, and fully-hardened H13 tool steel. The material used will depend on your specifications, the type of resin and the quantity of parts you want to produce.
● Steel Tooling
Steel tools are tougher and more durable but can take longer to produce. These are suited for larger volumes or when injecting abrasive or corrosive plastics that would damage aluminum molds.Pre-hardened tool steel is used for quantities from 100,000 , depending on plastic material and part geometry. We use P20 and NAK80 stress-relieved steel.Fully-hardened tool steel is the most durable and can be used for millions of injected parts. H13 hardened steel is ideal for full production volumes or when injecting abrasive engineering-grade plastics.
At DSW we have various tooling options available to you, offering different levels of capability from prototype through to short pre-production runs through to full production quantities.
We can provide you with:
● Low volume : Soft tooling for a few thousand cycles.
● Medium volume: P20 (pre toughened) tooling for up to 20,000.
● Higher volume : Fully hardened tooling in various guises up to 1,000,000 cycles maintenance free.
Where the cost of several mould tools would be prohibitive, we can offer Family tools that produce more than just one component design.
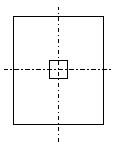 |
Single Cavity |
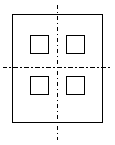 |
(low volume/low cost)
Multi Cavity
|
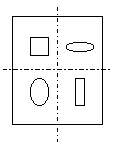 |
(lower component cost)
Family Tool
(lower tooling cost) |
All available in Soft or P20 or Fully Hardened tooling |
Construction Injection Molds Classification |
Classification or types of mold injection very depend on what we need to make the plastic parts, because every parts have specific and unique design. when design molds we must see what the influencing factor like geometry, number of cavities, ejection principle, plastic material and shape of parts.
The basic classification of mold based on construction shown on picture below
● Standard Molds
The standard mold is the most simple design, basically the standard molds is same as two plate molds construction, they divided in two side : cavity side and core side, cavity side is the side that construct to flowing plastic material from nozzle to cavity parts, basically they consist of sprue, runner. Core side construct to make shape for core, demolding system and ejection system, at this side we design ejection system. Standard mold have one parting line, and have one opening direction. this type of mold use in all kinds of plastic parts that doesn't have undercut, inner and outer screw. Light brown color little and straight in ejection system is shown ejector pin.
|
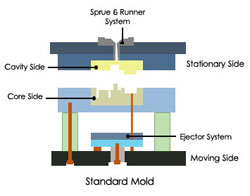 |
|
● Slide mold
Development from this mold type is the used slider parts in various molds types, basic slide mold is transfer horizontal movement of mold to vertical movement, this types of molds is used to make parts with undercut, you should see more at the post when we need slider for learn more.
|
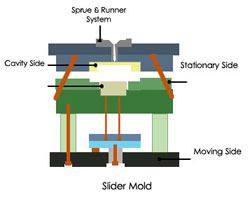 |
|
● Three plate molds
Basically three plate molds has two parting line, and floating plate, floating plate support by support pin, Since the mold has two parting planes, the runner system can be located on one side of floating plate or make special plate that attach in floating plate, we called runner plate, see post about runner plate.Three plate molds are used because of their flexibility in gating location. this types of molds is flexible even use in multiple cavity.
Note : floating plate also called cavity plate or plate number 3, to know more the different between two plate mold and three plate mold see the posting about Basic and Types Molds Construction |
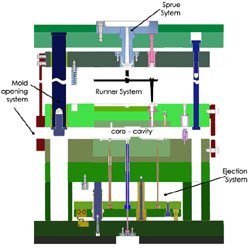 |
|
● Split Cavity Mold
Basically the split cavity is same as 2 plate standard mold, but the cavity have split block to make undercut product or external threads. This type of mold use when the slider is not enough to make the undercut or the threads. the disadvantages of this mold is when use for little parts, the construction will difficult.
|
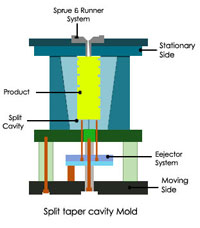 |
|
● Mold With Screw Device
This mold special to make thread forming, the core can be rotate when demolding process, both internal or external threads can be forming by this type mold.from those picture we can see that they have gear device, the gear will rotate when form thread.
|
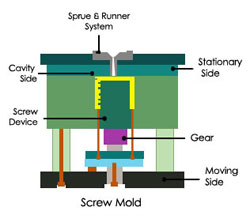 |
|
● Stripper Ejector Mold
This type of mold have special purpose to make a cup shape without undercut, stripper ejector will make ejection more easy, same movement and power at the product and without a lot of marks in product.
Molds with complex and difficult design can be integrated or combined one to the others mold type.
|
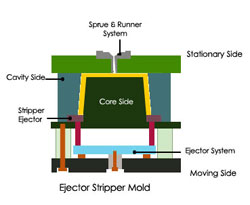 |
|
Moldflow Plastic Adviser, Plastics Insight, Moldflow Mpi, Mold flow communicator and Mold Adviser are Mould flow software products for simulating the injection molding of plastic materials. DSW use CAD Connectivity Tools to link structural CAD - CAE to MPI, MPA and MPX Community projects in the plastics and tool making industry. |
 |
|
After plastic design elements and cost elements have been considered, it's time to get the plastic molded. This step is done entirely on the part of production team. After all,DSW is not a consulting or design firm, but also a trouble shooter and analyses technician. The steps of the molded plastics production process are carefully planned and adhere to industry certification standards. In addition, customers get the benefit of experienced plastics engineers working on their component part. The plastic is cooled and packaged after molding.
International Standard |
|
AISI |
DIN |
LOCAL/ (JIS) |
Unit |
IN/LB |
MM/KG |
MM/KG |
Moldbase |
DME |
HASCO |
LKM/FUTABA |
Steel |
H13
420
P20
D2 |
1040
S-7
A2 |
1.2344
1.2083
1.2311
1.2739 |
1.2343
1.1730
1.2510
1.2767 |
NAK55,NAK80,DC11
LKM818H,LKM738H
LKM420,LKM2344 |
Component |
DME |
HASCO |
LKM |
Knock Out Location |
7",4x16",6x28" |
200,100 x 400 |
200,100 x 400 |
British Standard Pipe Thread |
NPT |
MM/BSP |
MM |
Location Ring |
⊄4.000" |
⊄100/110/125MM |
⊄100MM |
Sprue Radio |
R1/2",R3/4" |
R10, R15,R40,90° |
R15,R40 |
Thread |
UNC |
MM |
MM |
Ejector Pin |
DME |
HASCO |
|
Sleeve Pin |
DME |
HASCO |
|
Spring(Pressure Ratio) |
ASSOCIATE |
DAIDO,HASCO |
ASSOCIATE DAIDO |
Hot Runner |
INCOE,DME,Husky,Mastip |
HASCO,Synventive, Mold-Master,thermoplay |
Yudo Or Local |
Hydraulic Cylinder |
MILLER/PARKER |
PARKER |
Taiwan Or Local |
Gear |
DP |
"Module"-MM |
"Module"-MM |
Texture |
Mold-tech |
Mold-Tech |
Yixin or other local |
LOOK FORWARD TO YOUR SINCERE COOPERATION |